Building the future of speed? We get you there faster.
Redefining leading-edge engineering and manufacturing since 1922, our focus is on the research, development, and creation of advanced mechanical and electro-mechanical clutch systems.
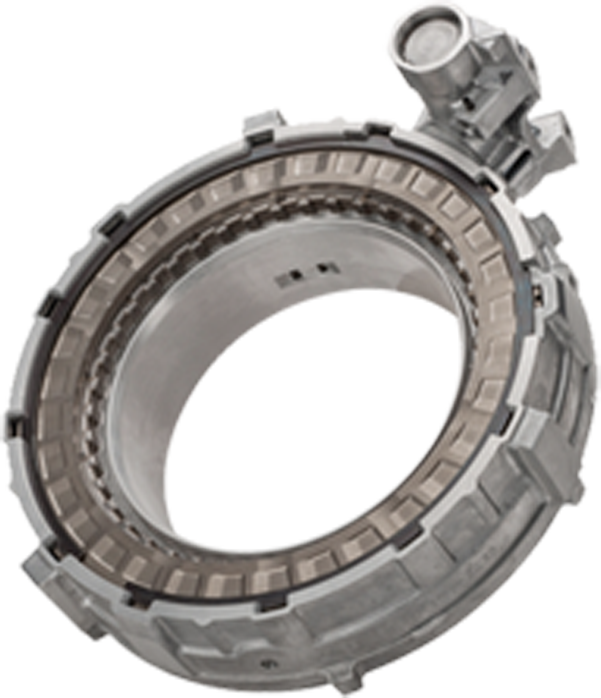
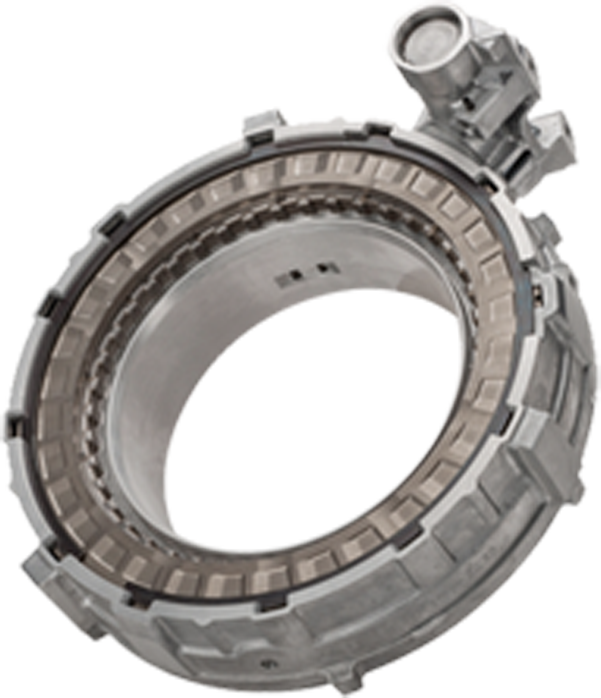
Controllable Mechanical Diode (CMD)
With outer race fixed into the transmission case, this mechanical clutch can be turned on or off.
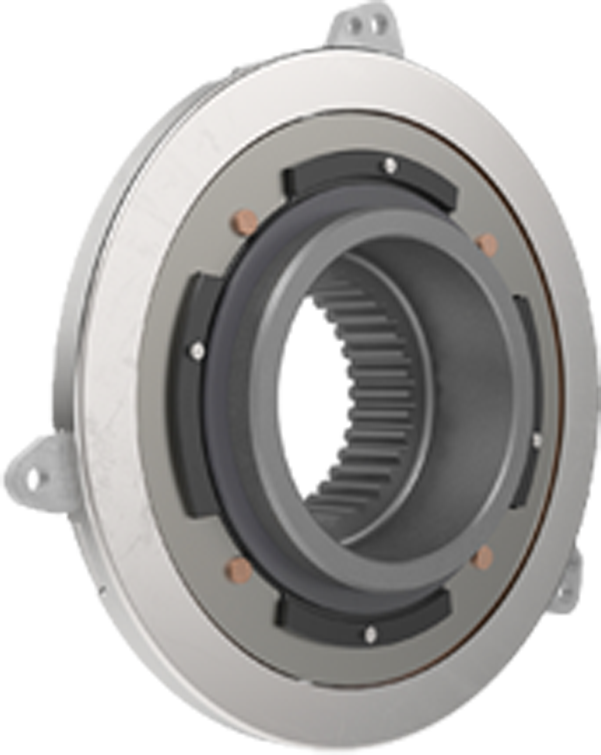
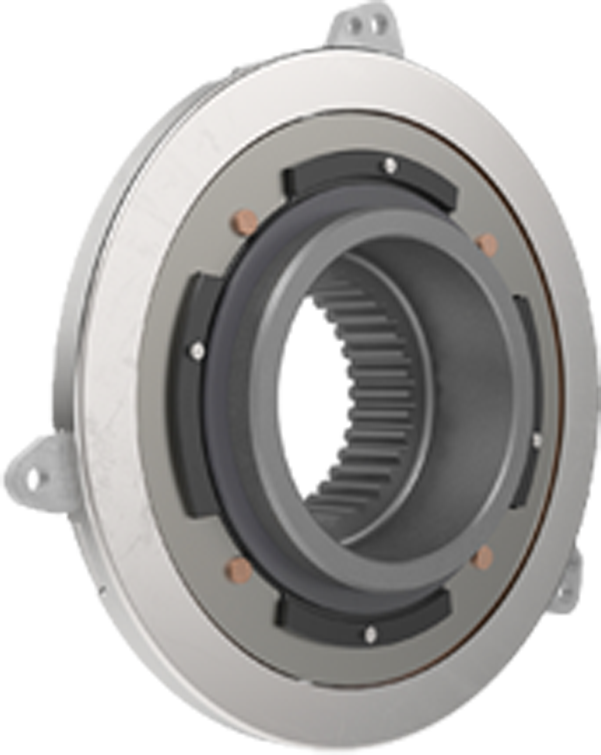
Dynamic Controllable Clutch (DCC)
This DCC has an outer race that spins within the case of the transmission.
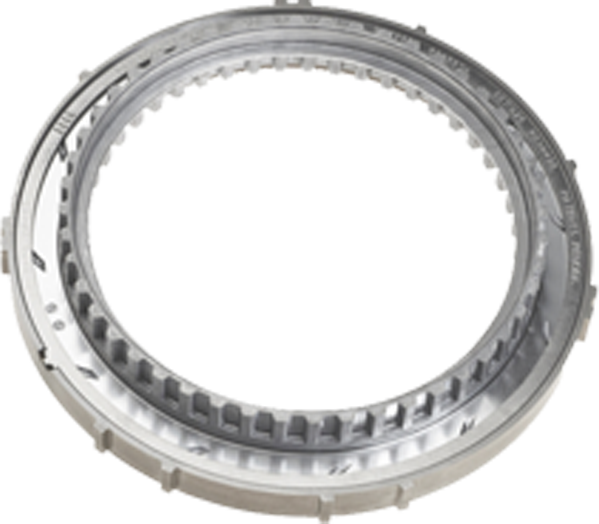
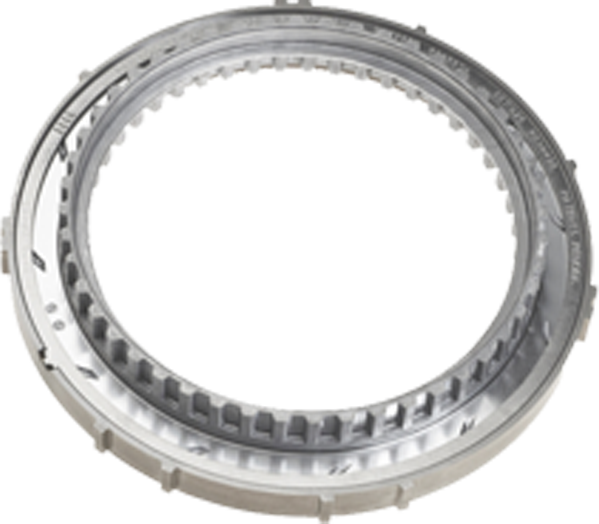
Mechanical Diode (MD)
This passive one-way clutch device leverages struts and compressive forces to carry torque.
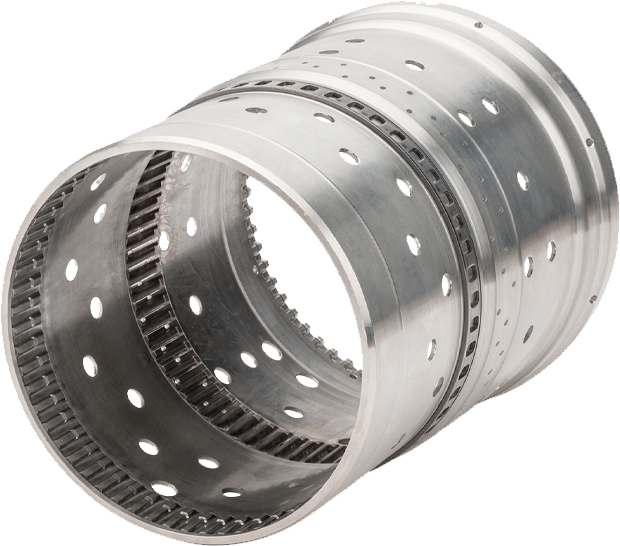
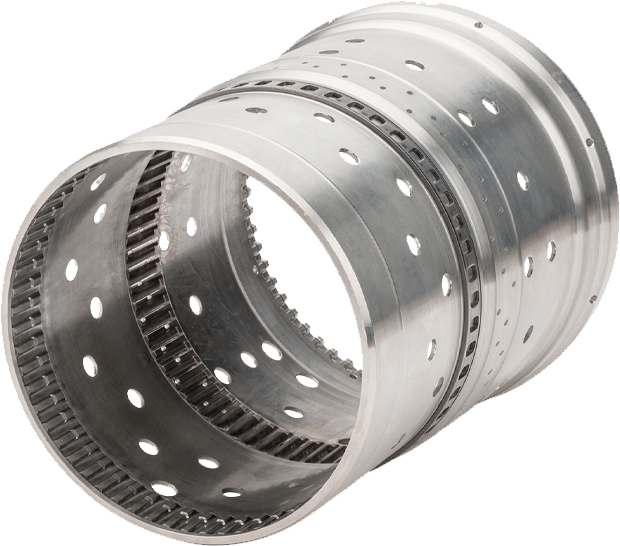
Advanced Metal Forming
Our leading-edge metal forming processes deliver market innovations in roller-die technologies. We developed the first aluminum flow forming process to the auto industry—introducing hoop-band forming to the manufacturing world.
All of our technologies, especially our first-to-market innovations, enable our customers to design lighter, more efficient e-drive and driveline systems. We also consult with our customers to help design systems that save costs, improve performance, and drive value for stakeholders.
This makes MEANS the supplier of choice for OEM and T1 Propulsion System engineers.
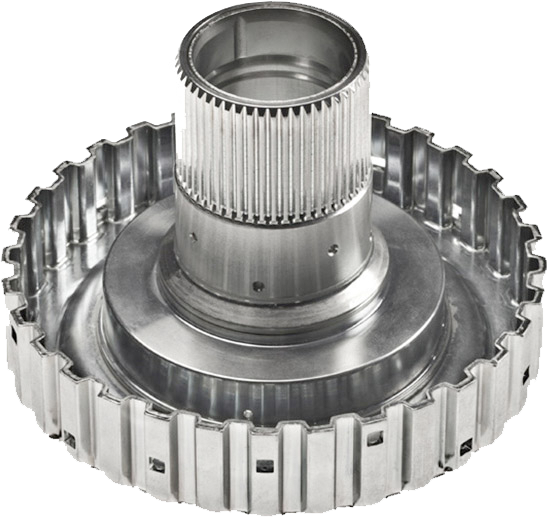
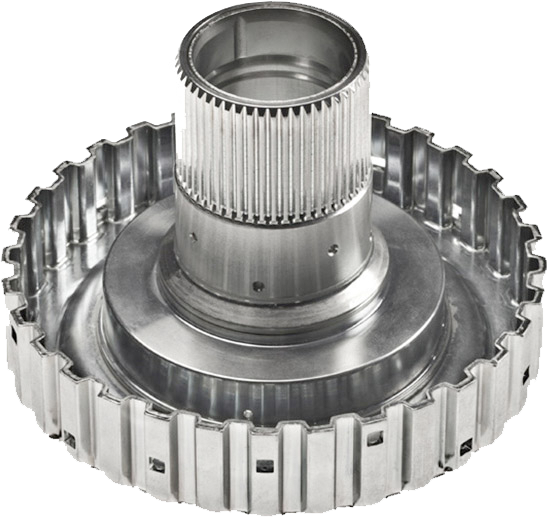
Welded Assemblies
An industry leader in integrated complex metal forming assemblies, our unique ability to design and develop innovative metal forming solutions, we help our customers surmount challenging geometries and project requirements.
Our years of experience and vertical process integration allow us to offer customers unique value when it comes to complex assemblies
Our mechatronic clutch technologies provide outstanding solutions for emerging EV propulsion systems – additionally, our vertically integrated advanced metal forming and powered metallurgy capabilities allows us to design and scale high-performing, cost-effective system solutions for leading OEMs.


Park Lock Hill Hold Systems
Means technology can be integrated directly into the system—delivering not only park lock but also hill hold and shifting solutions for traditional, hybrid and BEV architectures.


Multi-Speed Shifting
Means multi-speed shifting propulsion systems integrate with our CMD, DCC, and MD technologies – delivering seamless shifting solutions for traditional, hybrid and BEV gear boxes.


Transmission Powershifting
Means technology integrates directly into the drive system—delivering seamless shifting solutions for traditional, hybrid and BEV gear boxes.


Driveline Disconnects
Means’ driveline disconnect solutions provide a novel way to efficiently engage and disengage rear electric drivetrains from their half shafts—conserving energy and extending vehicle range.
This disconnect technology enables our customers to develop on demand AWD electric vehicle with full on-road and off-road capabilities, matched by uncompromising performance and efficiency.